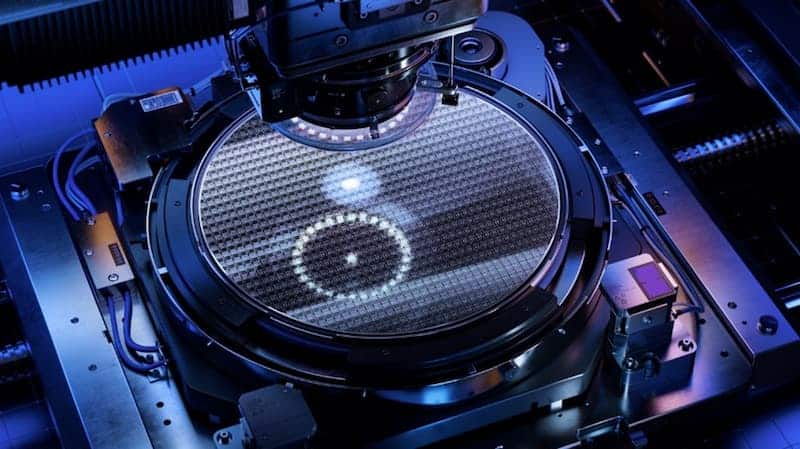
Nanosprings: Engineering on a Small Scale
Electrical components get increasingly smaller each year, but it’s hard to comprehend the manufacture of nanoscale springs for electrical devices.
Home › Science
Electrical components get increasingly smaller each year, but it’s hard to comprehend the manufacture of nanoscale springs for electrical devices.
Initially developed in the 1940s for jet engines, superalloys have come a long way since then, emerging as highly versatile
Springs are integral to a wide range of applications across an equally large number of industries, from automotive to power
Springs are key components found in an enormous amount of machinery, vehicles, and countless other complex systems across various industries,
The power industry’s non-negotiable foundations are extreme precision, reliability, and efficiency. These combined guarantee stable power generation and distribution consistently,
Robotic technology is certainly one of the most fascinating branches of electronics, constantly delivering advancements that we could only imagine
In the power industry, the quest for efficiency, reliability, and, above all, safety is constant. With its complex machinery and
Sustainability has become the world’s foremost concern, encompassing every industry and a wide variety of practices. With this heightened attention,
In the healthcare industry, where precision and reliability are paramount, one might not immediately think of springs as fundamental players.
And even if we don’t have exactly the tool we need, European Springs’ in house technology enables us rapidly to design and make complex tools, allowing us to offer more competitive prices.
© Copyright 2025 | European Springs
Designed, Promoted and Powered by SQ Digital