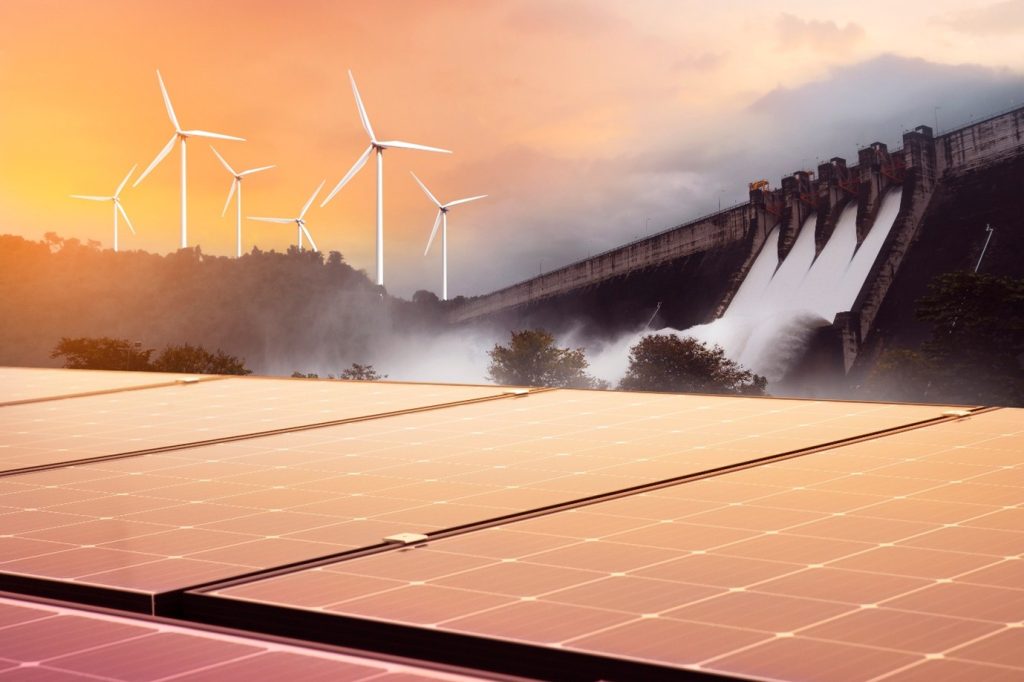
Springs and Pressings in the Clean Energy Sector
Components in the clean energy sector play a crucial role in shaping a more sustainable future for power generation. Springs
Home › News & Updates
Components in the clean energy sector play a crucial role in shaping a more sustainable future for power generation. Springs
Safety is our top priority at European Springs and Pressings, and we are committed to ensuring our team is fully
The 10th to the 16th of February is National Apprenticeship Week, and here at European Springs and Pressings, we are
The performance and longevity of a spring depend not only on its quality but also on proper maintenance and regular
At European Springs and Pressings, we are dedicated not only to delivering high-quality products but also to ensuring they are
Springs play a crucial role across a wide range of industries, from supporting intricate mechanisms to powering heavy machinery. Perhaps
Melinex is a durable, heat-resistant material widely used in bespoke pressings and stampings across various industries. Its reliability and versatility
At European Springs and Pressings, we implement several procedures during our manufacturing process to ensure that the springs we create
At European Springs and Pressings, we prioritise high-quality and consistent manufacturing practices in all of our products. As expert spring
And even if we don’t have exactly the tool we need, European Springs’ in house technology enables us rapidly to design and make complex tools, allowing us to offer more competitive prices.
© Copyright 2025 | European Springs
Designed, Promoted and Powered by SQ Digital