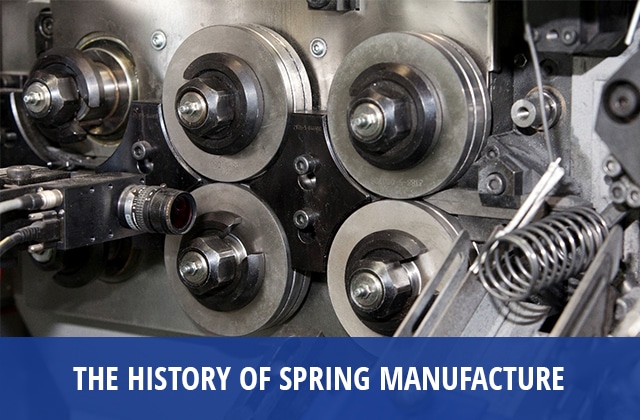
The History of Spring Manufacture
You may not realise how many times a day you use something that requires springs to work. From light switches
Home › Engineering › Page 14
You may not realise how many times a day you use something that requires springs to work. From light switches
In engineering, it’s vital to ensure that products are optimised to the highest of standards (and with the utmost trust).
On Tuesday, 11th July, the British Government announced a huge increase in the UK satellite sector. This boost will see
The engineering industry is always requiring skilled workers to ensure the continuation of its development. Modern society requires the input
The world of engineering is fast paced, it is something that we here at European Springs know well and live
The spring has been bouncing into businesses since the early 15th century, and manufacturers, engineers, scientists and even artists have
Producing a three-dimensional model of a product alongside a digitally-rendered visualisation, modern rapid prototyping projects are created through additive layer
There are numerous talented individuals who have created inventions and brought new ideas that have changed the world. Transport such
Whether developing a completely innovative design or remaking one for optimised results, in engineering it’s vital to ensure only the
And even if we don’t have exactly the tool we need, European Springs’ in house technology enables us rapidly to design and make complex tools, allowing us to offer more competitive prices.
© Copyright 2025 | European Springs
Designed, Promoted and Powered by SQ Digital